Industry News, Coatings
Sustainability in the Coatings Industry
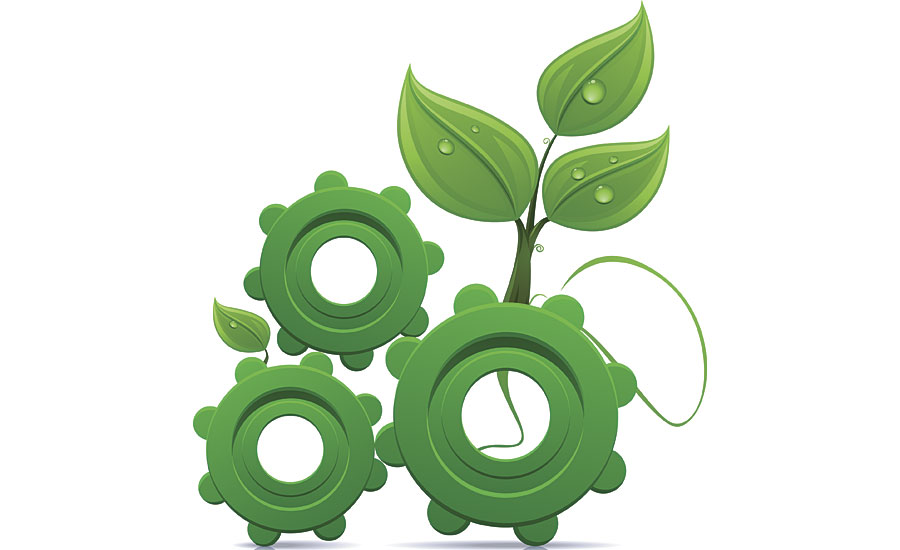
Industry News, Coatings
Link: Sustainability in the Coatings Industry | PCI
By: Tony Mash
The coatings industry worldwide has been addressing the three pillars of sustainability for some years, and considerable progress has been made. Some of this improvement has been driven by legislation and some designed to address specific customer needs. There have also been examples of voluntary initiatives by companies with a strong environmental ethos.
Over the last two years, companies supplying the industry and coatings companies themselves have been recognized by independent third parties. AkzoNobel has been ranked as the leader in the Dow Jones Sustainability Index for the Superchemical sector in 2012, 2013 and 2014. Dow Chemical has received the U.S. Presidential Green Chemistry Challenge award for the development of precomposition polymer technologies that can partially replace TiO?, and Becker Industries1 received the Sustainable Innovation Award from the British Coatings Federation for its work on high solar reflectivity and emissivity coatings for use in the construction industry.
Formulation production improvements have been tracked in a measured way by adherents to Coatings Care®.2 Reductions in injuries, energy consumption, solvent usage, volatile emissions, and waste and shipments to landfills have been confirmed over the past 15 years. The industry has met the demands of an increasingly regulatory environment by reducing VOCs in formulations and, in Europe, observing the regimen of REACH and specific country regulations, such as those in France.
While these developments are all very laudable, many of these initiatives would have been made anyway as part of companies’ business-as-usual strategies. Companies undertook many of the past improvement measures to reduce cost and enhance competiveness, and did not need to cite sustainable development to justify their innovations and investments.
Trade Associations such as CEPE,3 the ACA,4 FIPEC,5 and the BCF6 have published brochures that extol the decorative and protective qualities of coatings. These impressive documents defend the existing stance of the industry on the issue of sustainability, provide some excellent examples of best practices, and commit in broad terms to further improvements to help promote the image of the coatings sector to external bodies that wish to know where the industry’s values lie.
Given that sustainable development has been on companies’ agendas for a number of years, it runs the risk of being eclipsed by more topical initiatives. In political terms, It may be the case that energy sourcing and economic recovery have overtaken sustainable development as priorities, particularly in the United States given the attractiveness of domestic shale oil and gas deposits. One can also conjecture that the technical low-hanging fruit has already been picked by the coatings industry, leaving only the risky, technically challenging and investment-intensive developments left to attack.
The inconvenient truth is that the issues that prompted the UNEP Climate Change conferences of 1992 and 2012 have not gone away and still need to be addressed. World population will rise from its current 7 billion to 9 billion by 2050. Sources of the majority of raw materials used by the coatings industry are finite and need to be husbanded carefully. The concentration of carbon dioxide (CO?) in the atmosphere has grown to levels not seen for 3 million years, and about half of cumulative anthropogenic CO2 emissions between 1750 and 2010 have occurred in the last 40 years.
Continuing to deal with business-as-usual issues alone, while prudent corporate tactics, will not lead to the kind of paradigm shifts that are needed to ensure that the coatings industry maximizes its contribution to global sustainable development. In the words of Professor Michael Braungart of EPEA,7 we need to focus on eco-effectiveness rather than eco-efficiency. “Doing the right things rather than doing things right” will speed our way towards a totally sustainable industry.
Here are some of the ways the coatings industry can move forward beyond business-as-usual.
Paradigm shifts often require out-of-the-box thinking or a sudden breakthrough that was not anticipated. Chance discoveries are often the key to progress and can play an important role in creating new technologies.
It is generally accepted that 10% of the environmental footprint of coatings is created during formulation, with some 50% generated upstream under the control of the raw material manufacturing industries, and 40% created downstream in use and disposal. However, through its choice of ingredients, the industry can impact the footprint of the whole supply chain.
In order to make the right choices, the industry cannot act alone, but must work hand in hand with its upstream supplier networks that take materials from the ‘cradle’ and supply materials ready for formulation to the paint manufacturer’s gate. In designing the coatings of the future, the paint manufacturers must also understand downstream requirements of paints, their modes of application, the anticipated roles to be played by the coatings and the ways in which coated products are disposed of, once no longer required. Put another way, one must avoid thinking in silos from gate to gate but broaden one’s sights to take account of the full impact of coatings from raw material cradle to grave.
To address this need, the chemical industry has organized a global supplier engagement program entitled Together for Sustainability (TfS).8 Its goal is to assess and improve sustainability sourcing and reporting practices, including ecological and social aspects. This group includes major global chemical companies that supply the coatings industry as well as coatings companies such as AkzoNobel and BASF.
The impact of sustainability extends beyond the grave! The regenerative circular economy espoused by the Ellen MacArthur Foundation9 calls for life cycles of all products to be designed in ways that recover materials for reuse either through technical or biological recycle routes. To use a phrase authored by Professor Michael Braungart,7 “waste equals food.” It is critical in disposal activities to safeguard nutrients and not destroy them, so that they can be of value to society again and again. The mantra changes from ‘cradle to grave’ to ‘cradle to cradle’.
The coatings industry, therefore, needs to ensure that the ingredients it uses contain only materials that will not harm the environment or society either in application or recycle. This principle has been best addressed to date by Clariant through the Eco-Integration element of its Ecotain® concept10 by which the company endeavors to offer dispersing agents that leave behind a very small footprint in both use and disposal.
Another feature of this life cycle model is that not only should there be no boundaries between industries in the supply chain, there should also be no country or continent boundaries. We all live in one global environment with one set of finite sources of raw materials. It is imperative that we manage our journey towards full sustainability in a consistent way, sharing knowledge, agreeing to the same technical targets, applying the same processes and utilizing the same measures to monitor progress. Without a level playing field, progress will be continually impeded by confusion in the market place and mistrust within the coatings industry. As an example of confusion, ISO 16000 and ASTM D 6886-14 do not currently share the same definition of a VOC in coatings formulations.
The global construction industry has developed a process that the coatings industry should consider adopting. It has organized Green Building Councils in most countries of the world coordinated through the World Building Council11 drawing on global standards such as EN 15084.
Trade Associations in Europe and North America are working well together either through IPPIC12 or via the committees supporting the Paint Pilot organized by the EU’s Product Environmental Footprint project in Europe.13 One needs to see this active coordination increased to include Asia and South America to ensure a globally consistent approach to sustainability.
It goes without saying that society has to be willing to pay for product improvements and enhancements. It is only occasionally when there is an urgent, unfulfilled demand that there will be potential opportunities for price premia and margin enhancement. New technology is often linked to high cost; a reasonable assumption given the expense of research and the likely absence of low-cost routes to manufacture due to early lack of scale.
Process streamlining can help reduce the cost of innovation and implementation. The TfS program is targeted to offer one set of sustainability audits to address the enquiries of potential customers in a cost-efficient way. AkzoNobel,14 which has recently joined the TfS program, has launched its Planet Possible™ corporate program, which sets out to ”do radically more with less.”
Leading companies inside and outside the coatings industry are devoting significant resources to social outreach and support programs to:
Such processes, often an essential part of corporate manufacturing strategy, can also impact the successful marketing of a company’s products and services. There are examples of companies that have used communication with the consumer to increase awareness of sustainability issues, prompting pressure back on industry to make changes to its products and processes.
It has been said that when price and quality are equal among competitors, brand choice can be based on corporate social purpose.
At the end of the day, the consumer is the driving force behind any change. The design of future paint products needs to take account of broad social trends. Companies would be well advised to continually monitor alterations in the values of society, prompted by issues such as increasing global population and energy availability that impact subsequent lifestyle changes. Some broad societal issues will have an impact on new product development, such as:
The petrochemical, plastics and chemical industries provide the majority of the materials used by the coatings industry and represent a key element of the coatings environmental footprint. These suppliers have a solid record of continual manufacturing efficiency improvements and new product innovation. Indeed, the specialty chemical industry has been reported by A.T. Kearney as spending more on R&D compared to sales revenue than the coatings industry.15
Novel chemistry has an important part to play in environmental footprint reduction. Recent examples include:
Bio-renewable technologies have been known for many years and are receiving increasing attention of late as sustainability increases in priority. AkzoNobel14 has committed itself to doubling the renewable component of its raw material purchasing slate by 2020.
The use of bio-renewables cannot only reduce the environmental footprint of downstream products but also extend the diversity of supply sources of formulation ingredients. It would be commercially prudent to find bio-renewable alternatives to existing formulation ingredients to cover the situation when oil and its downstream products such as resins ever go short, as they did in 2008/2010.
Although concern has been expressed about drawing raw materials from the food chain (first-generation sources) to make bio-renewables, others have argued that the impact on the world supply of food is and will continue to be insignificant.
Some bio-renewables have demonstrated the potential to offer improved property profiles due to their often more complex structure than the materials they are replacing; an important selling point for those in the business-as-usual paradigm.
Examples of bio-renewables of interest to the coatings industry are:
Corbion Purac19 supplies lactide building block chemicals made by the fermentation of sugars that can enable polyester resin producers to create modified resins with improved property profiles in their final application.
North Dakota University20 has developed biobased polyvinyl ether copolymers from soya bean oil and menthol, which provide product enhancements ideal for alkyd coatings.
Eindhoven University of Technology, Holland and Imperial College, London, UK21 have recently reported discoveries of innovative catalyst systems that make possible the polymerization of a range of resins incorporating carbon dioxide, without the help of enzymes. Some of the resins produced by these mechanisms “are promising as binders in industrial paint formulations.”
Bayer22 has developed tailor-made polyether carbonate polyols from propylene oxide and carbon dioxide.
Brown University23 has made a breakthrough in the manufacture of acrylates using ethylene and carbon dioxide with nickel as a promoter.
With carbon dioxide as one of the products generated by the decomposition and incineration of coatings, the regenerative circular economy can be exemplified by its re-incorporation in resins and binders.
The location and sourcing of raw materials, energy and water, together with the efficiency of ingredient manufacture can have a significant impact on the footprint of coatings formulations.
Just as the specialty chemical sector is helping the coatings industry address sustainable development by the provision of new, more sustainable ingredients, the coatings industry needs to help its downstream industries address their own sustainability targets.
In the decorative retail sector, it is recognized that consumers tend to purchase more paint than they need, and there are significant quantities of waste paint unused and slowly deteriorating in homes. Programs have been launched, for example, in Canada, the United States,24 France, U.K. and Holland to collect waste paint, and reconstitute and blend them ready for resale and use. Such programs require close coordination and support from local governments.
With the regenerative circular economy in mind, coatings have a key role to play to enhance the recyclability of their substrates.
Downstream sectors such as the packaging, automotive and furniture industries have built businesses around the recycle of used parts, sometimes enhancing the value of the original coated product. In its second and subsequent cycles, coatings manufacturers need to support downstream industries by ensuring that there are no toxic chemicals or intermediates created in the recycle loop that prevent safe processing of the substrate into its new form.
With 40% of the environmental footprint downstream of the factory gate, improvements in paint performance can have a significant impact on the sustainability of the entire life cycle. In the context of industrial coatings in which substrates such as metals and wood are protected, enhanced lifetime of the coating is a major benefit.
The iconic example is the coating of the Forth Rail Bridge in Scotland using paints from Sherwin Williams25 that have a claimed lifetime of 25 years. Gone are the days when this long bridge had to be continually repainted from one end to the other.
As innovative coatings are developed with increasing longevity, manufacturers will need to verify that persistent chemicals that can cause harm to society or the environment are not introduced or developed.
Coatings can do more than decorate and protect, and enhanced functionality can bring significant improvements to the sustainability of downstream industries, particularly in areas where energy reduction is a valued goal. Examples are:
It has often been said that if you cannot measure progress, you cannot manage it. The tracking processes within Coatings Care2 are excellent ways of looking at elements of formulation manufacture and can demonstrate examples of increasing eco-efficiency from gate to gate.
On a broader front, Life Cycle Analyses have been used by some companies such as Dow, Solvay, BASF and DSM to promote their new products. This form of analysis does not solely look at carbon footprint but addresses a wide range of other environmental and toxicological variables that have relevance to the manufacture and use of coatings.
CEPE3 has provided its membership with software that can provide Life Cycle Analysis evaluations together with a unique LCI database of the ingredients most often used in paint and ink formulations. A few companies, such as DSM,26 have used LCAs publically to compare different processes for achieving desired coating performance, but it would be fair to say that the use of this approach is still in its infancy.
The EU, through its PEFCR project,13 is endeavoring to put together a methodology that will provide objective comparison analyses that do not leave conclusions open to wide interpretation. To its credit, the coatings industry has been chosen to be in the first wave of such pilots, and CEPE is chairing this particular pilot, with the anticipated output of objective and measurable Product Category Rules (PCRs) for decorative coatings.
The TfS global initiative is committed to improve and assure the quality of sustainability assessment and audit results.
The analysis frameworks are available. We now need to see some conclusions drawn from these processes to understand where the hotspots are from one end of the supply chain to the other, so that decisions can be made on the preferred sustainable coatings systems of the future.
The coatings industry has made a good start but has further to go on its path of sustainable development. The opportunity for significant progress in the future lies beyond business-as-usual. The recommended course of action is to:
Reference to Cradle to Cradle® by kind permission of Professor Michael Braungart of EPEA.
1.Becker Industries/BCF award
2.Coatings Care
3.CEPE Sustainability Charter
4.American Coatings Association Sustainability brochure
5.FIPEC Environmental Charter
6.British Coatings Federation Sustainability Policy 2009
7. EPEA: Eco-effectiveness
8.Together for Sustainability (TfS)
9.The Circular Regenerative Economy model
10.Clariant Ecotain® concept
11.World Green Building Council
12.IPPIC
13.PEFCR project
14.AkzoNobel Sustainability strategy
15.A T. Kearney analysis of the Coatings Industry’s R&D intensity
16.Dow on Sustainability
17.Arkema on novel resins for coatings
18.Solvay on TiO2 partial replacement
19.Corbion Purac Lactide products
20.North Dakota University enhanced Alkyds
21.Eindhoven University of Technology and Imperial College London
22.Bayer on polymerization with CO?
23.Brown University on polymerisation with CO?
24.Paint Care® Waste Paint recycling in the USA
25.Sherwin Williams Forth Rail Bridge example of coatings longevity enhancement
26.DSM Comparative Carbon and ECO Footprint Study on liquid vs Powder Industrial Finishes for MDF. Authors; Jos Verlaak, David Morris, Proceedings 8th PRA Woodcoatings Congress 2012 Amsterdam.