Industry News, Coatings
Modern Organic Thixotropes
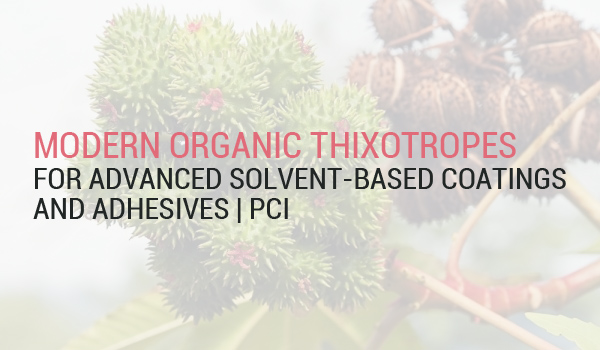
Industry News, Coatings
Link: Modern Organic Thixotropes | PCI
By: Elementis
Hydrogenated castor oil is a good organic thixotrope or rheological additive (RA) because excellent performance can be obtained from this wax, provided that the additive is dispersed and activated in a specific manner. The rheological additive provides anti-settling effects, and controls flow and levelling, as well as the degree of sagging in coatings. The glyceride moiety in castor wax can be replaced by amine functional materials to yield wax-like amides of 12-hydroxy stearic acid. These amides are also quite effective as rheological control agents, and they complement hydrogenated castor oil to yield an effective castor wax portfolio of materials for the paint formulator to choose from. The castor-derived 12-hydroxystearic acid moiety is an effective rheological component because it can self-assemble into spatially preferred structures, some of which extend throughout the formulation and effectively trap solvent and/or resin, and thereby control the material flow. An example of such a network is shown in Figure 1.
Figure 1. SEM micrographs of amide-based castor waxes showing (A) additive powder before incorporation, and (B) the synthetic rheological additive after full activation. ©PCI
Finely milled powders of castor wax must be subjected to solvent wetting, de-agglomeration and high-shear dispersion forces at specific temperatures to unlock rheological benefits. Castor wax-based rheological additives have specific processing temperature requirements that are related to the solvency that are present in a paint system. Therefore, the most appropriate choice of castor-based rheological additives for any given system depends on solvent type(s), processing temperature control and the manufacturing equipment. An optimal combination of these parameters allows for the most effective level of colloidal dispersion and yields a rheologically active network. With proper use, a castor-derived rheological additive provides outstanding efficiency for thixotropic (shear thinning) viscosity build, sag control and pigment suspension.
However, problems can arise when the paint processing temperature is too high for the additive – the castor wax can dissolve completely at these elevated temperatures and later on, as the system cools down, the additive can precipitate and form semi-crystalline particulate matter, which is sometimes also referred to as “seeds.” A similar seeding situation can occur when the solvent/temperature combination is too strong. The immediate seeding effect typically can be observed relatively quickly. A more complex seeding situation occurs when the additive is not processed enough. In these cases, not all powdered wax material has been converted into the desirable rheologically active form, and unused material remains behind, often unnoticed at the point of paint manufacture. Over time upon storage, this unused additive material can transform under the influence of solvent, ambient temperature and time, to yield particles that lead to loss of fineness of grind and reduced gloss. The above-mentioned amide-based castor wax derivatives have mostly overcome this seeding problem. An effective range of products is available, provided that the paint processor has equipment controls and capabilities able to handle these materials in the preferred manner.
The anti-sag resistance and viscosity build of coatings containing synthetic rheological additives based on castor oil can depend on the paint and adhesive processing conditions used to incorporate them into the paint. Some of these important conditions include temperature, mixing time, shear rate and the cooling schedule of the manufacturing batch. Additionally, raw material ingredients within the coating formula have also been found to either positively or negatively affect this performance. For instance, certain fillers can enhance the performance. Conversely, particular additives that are in the classes of defoamers, dispersants, wetting agents and amine curing agents for epoxies can at times detract from the performance of the rheological additive. Some attention should be given during the formulation step to carefully select and optimize these ingredients.
In order to demonstrate and gauge a few of these effects, model paint preparation experiments were performed. A 90%-solids industrial-type 2K epoxy paint was used as the base coating system. The generalized formula is shown in Table 1. The curing agent used for part B was a blend of a phenalkamine and an amidoamine. Solvent was varied in order to examine its effect on RA performance. In some instances, the percent solids was raised to 95% or 100% solids. The RA loading in the paint formula was fixed at 1% based on total solids weight in order to visualize differences. This may result in sag resistance levels that are not commonly found in commercial applications. A generally recommended process for the incorporation of RA into a paint is to add the initial charge of resin, solvent and RA to a mix tank. This mixture is then pre-dispersed at 15-20 m/s for a specified amount of time. After this pre-dispersion step, fillers and dispersants are added and then the mixture is further dispersed at 15-25 m/s and at a specified batch temperature until a particular fineness of grind is achieved.
Component A | Component Supplier | Parts by Wt. |
Bis-A epoxy resin | Miller Stephenson (EEW=187.5 g/mol) | 23.52 |
Epoxy reactive diluent | Cardolite (alkylphenol glycidyl ehter; EEW=137.5 g/mol) | 1.97 |
Rheological additive (RA) | Various suppliers | 0.90 |
Solvent | Various suppliers | 9.68 |
TiO2 filler | Chemours | 6.77 |
Talc filler | Imerys | 8.39 |
Sodium potassium aluminosilicate filler | Unimin | 6.77 |
Anti-corrosion pigment | Heubach (zinc-containing filler) | 1.67 |
Calcium silicate filler | NYCO (epoxy surface functionalized filler) | 7.62 |
BaSO4 filler | Cimbar | 14.39 |
Defoamer | Elementis Specialties (non-silicone aliphatic) | 0.31 |
Colorant | Elementis Specialties (black pigment dispersion) | 0.13 |
Component B (blend) | ||
Amine curing agent | Cardolite (phenalkamine; AHEW=132 g/mol) | 11.49 |
Amine curing agent | BASF (C18 unsturated fatty acid amidoamine; AHEW=95 g/mol) | 5.74 |
A RA’s performance in a paint or sealant is evaluated with a number of possible test methods, depending on the type of coating and the particular end application industry. These tests can include the Leneta anti-sag test, Channel sag, Boeing slump, extrusion rate, adhesive viscosity increase and rheometric shear recovery tests. The results that will be presented in this article will focus primarily on the Leneta anti-sag test (ASTM D4400). An initial performance evaluation was conducted 24 hours after paint manufacture (initial), and after seven days of accelerated oven aging at 120 °F (accelerated aging).
The Leneta anti-sag-resistance test uses a notched drawdown bar in a low-shear method to apply the coating material. Typically, a painter in the field spray-applies an industrial paint on a vertical surface, such as the exterior of a bridge or the interior of a storage tank. Spray application is a high-shear operation that could potentially impact the rheological recovery of the paint and lead to different results. However, for work in a laboratory setting, the Leneta anti-sag test that is done by performing a drawdown on a test chart is a quicker and more convenient way to evaluate the sag resistance of a prepared paint than spray application. Figure 2 shows the sag results of two paints each made with a different industrial RA. Both paints had their sag resistance determined by spray application and also by drawdown application. The results of this comparison are shown in Figure 2. These show that the sag resistance results from the drawdown method used in this study are similar and do correlate reasonably well with a typical airless spray application. This gives more confidence that the lab-produced sag resistance performance data of the RAs discussed in this article has practical meaning in real-world application processes.
Figure 2. Comparison of sag resistance determined by both spray and drawdown application for two paints made with different industrial RAs ©PCI
Paint manufacturers use a variety of solvents in their formulas and quite commonly use mixtures of solvents. The variation in solvent type can have a dramatic effect on whether a RA will provide the anti-sag property needed. Some RAs are not suited to work well in certain solvents. Figure 3 shows the results of an experiment that highlights some of the effects of solvent and the incorporation temperature for a 95%-solids epoxy paint formula made with a commercially available industrial RA. All paints were prepared using a RA loading level of 1% based on total solids. Two different temperatures (120 °F and 150 °F) of the milling step were used to cross-correlate that effect with the solvent effects. Additionally, removing the solvent completely from the formula yielded a 100%-solids epoxy coating formula that was also included in the evaluation. The 100%-solids results are potentially applicable to adhesive applications.
Figure 3. Impact of solvent type and paint preparation temperature on initial and accelerated sag resistance of epoxy paints. ©PCI
For this particular RA, the results shown in Figure 3 indicate that it produces the strongest anti-sag performance with butanol (BuOH) as the paint solvent at both incorporation temperatures. The initial performance is reasonably stable after accelerated aging. However, when methyl amyl ketone (MAK) or xylene is the paint solvent, the initial sag performance is greatly reduced relative to the BuOH. Based on the results, both the solvent type and the paint processing temperature have a strong influence on the RA sag resistance and accelerated aged performance stability. The removal of the solvent altogether for the 100%-solids coating reduced the sag resistance performance of the RA for both paint mixing temperatures at which they were prepared. These results are specific to this particular RA, paint process and paint formula. An idealized RA would be one that was robust and works well for a wide variety of formulas, processes and temperatures.
Following the let-down step there are several options that a producer could take as a last process step. These could include: (A) allowing the paint to cool with agitation prior to discharge; (B) discharging the paint at the elevated mixing temperature directly into pails or drums; and (C) allowing the paint to cool without agitation before discharging it out of the tank. Model paint experiment results demonstrating these effects are shown in Figure 4. Approach A, to cool with stirring before discharging the paint, resulted in significantly lower sag resistance performance of the final curing paint. Approaches B and C resulted in the strongest sag resistance, as measured in the final mixed A+B curing paint. This last manufacturing process step highlighted here can be significant when considering how to optimize the paint preparation process in order to obtain the maximum performance from the RA. When using pure castor wax-based products, approach A is the recommended method to avoid false body effects where viscosity is irreversibly altered upon further handling.
Figure 4. Influence of canning method on sag resistance. ©PCI
In current paint manufacturing, the processing conditions are adjusted (temperature, shear rate, time) to accommodate the characteristics of the currently available amide-based castor waxes. A preferred rheological additive is designed to allow for paint manufacturing procedures that can yield cost savings by reducing production time and energy costs (no additional heat requirement).
Stepping away from castor wax technology, organogelator additives have been developed that can self-assemble into platelets, colloids or fibrillar materials, which are the structures responsible for gelling a solvent system. The unique organogelator spatial structure directs the anistropic aggregation of individual molecules, which results in the formation of supramolecular fibers. The fibers further interact with each other and intertwine to give an interconnected network. As a result, various molecular engineering tools are available to design a next-generation additive that meets the above-mentioned targets.
An illustration of a next-generation additive that brings many of the desired performance characteristics is shown in the following example. The new RA is incorporated (mixed) into the high-solids polyurethane formula shown in Table 2. For comparison purposes, three commercially available industrial RAs were also evaluated in this experiment. The RA loading level for all RAs evaluated was 1.3% based on total solids of the A+B mixed paint. Pigment grinding was done for 30 minutes at 9.4 m/s, which is a relatively low dispersion speed. This formula benefits from a type of TiO2 that is easily dispersible at low mix speeds. No heat was added to the paint mix pots during mixing. Batch temperatures were measured at the end of the dispersing step and it was found that this low-shear-rate dispersion only raised the temperatures of the batches up to 80-85 °F, which is a marginal increase above ambient temperature. Existing commercial RAs typically require batch temperatures of 120-165 °F to activate the RA. Without adequate activation of the RA, the paint often exhibits large variations in both viscosity and sag resistance upon aging at elevated temperatures.
Component A | Component Supplier | Parts by Wt. |
Acrylic polyol in butyl acetate | BASF (modified rapid property development acrylic polyol, 80% solids in butyl acetate, eq. Wt.=400 g/mol; OH number=135-150) |
31.43 |
Solvent (methyl amyl ketone) | Various suppliers | 16.37 |
Levelling aid | BASF | 0.16 |
Rheological additive (RA) | Various suppliers | 1.02 |
TiO2 filler | Chemours (easily dispersable) | 39.33 |
Component B (Curative) | ||
Isocyanate curing agent | Bayer (aliphatic, 100% solids Eq. Wt.=183 g/mol; 23% NCO) | 11.69 |
Leneta anti-sag test results for this experiment are shown in Figure 5. These results demonstrate the low initial performance of the commercially available RAs in this coating system with these moderate-shear mixing conditions and with no added heat. Upon accelerated aging, those RAs appear to activate in the can and produce sag resistance results that are much different than initially right after production. This much rheological instability is significant and is a major production issue for paint manufacturers.
Figure 5. A next-generation, easy-to-use additive: RA activation at low shear and ambient temperature. ©PCI
In comparison to the results for the commercial RAs, the new RA produces strong initial anti-sag results, even under these very low-energy mixing conditions with no added heat. The stability following accelerated aging is also greatly improved relative to the commercial RAs. The new RA activates quickly and does not require a lengthy heat up period during paint or adhesive manufacturing. Reduced production time and energy costs can yield costs savings, while faster production rates and increased manufacturing capacity are valuable benefits as well.
Copyright of this article by PCI. We are sharing and promoting the market innovation.
If you like this article, kindly to visit www.pcimag.com