Industry News, Flavor & Fragrance Industry
Exploring the Benefits of Utilizing Turpentine in F&F
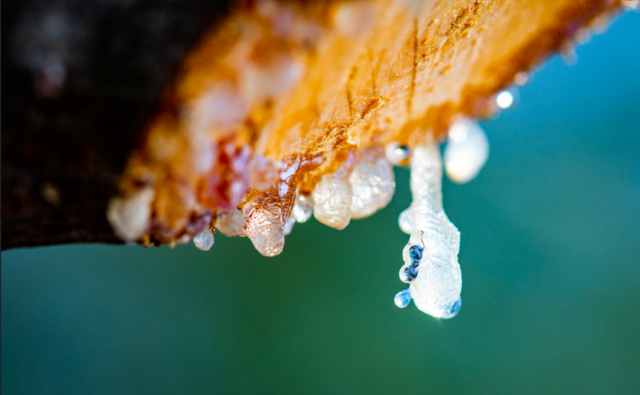
Industry News, Flavor & Fragrance Industry
Article by ISABELLA CAMPBELL, global marketing director, terpenes, Symrise
Pic by Nicholas Erwin, Flickr
Reviewing the production process and versatility of the renewable and sustainable F&F material.
The fragrance industry uses many natural ingredients, such as lavender, jasmine, sandalwood and centifolia oils. The perfumers’ palette also contains thousands of synthetic molecules. Since the development of the first synthetic F&F ingredients in the late 19th century, the chemical processes have evolved significantly. There are evermore synthetic options for perfumers and flavorists. These synthetic materials have allowed fragrances and flavors to become mainstream and accessible to mass1 They go into everything from high-end designer perfumes to laundry detergents and car scents. Today, industry estimates are that petrolderived ingredients comprise over half the raw materials used in flavors and fragrances.
The non-stop growth of social media has sharpened consumer awareness and increased interest in the source of ingredients used in products they use and purchase. This increased awareness, together with legitimate environmental concerns, is resulting in growing consumer interest and demand for products made from sustainable and renewable sources. Luckily, the fragrance industry can draw on the most abundant essential oil available in nature—turpentine. Turpentine is the volatile fraction of the oleoresin of coniferous trees grown all around the globe.
Worldwide, turpentine production in 2020 estimated to be 325,000 MT. Of this, about 60% undergo a conversion into F&F ingredients2,3,4 Three commonly used methods for the extraction of turpentine exist. Gum turpentine (GT) is obtained by tapping trees and collecting the exudates. Today, this source represents approximately 40% of the world’s available turpentine. Crude sulfate turpentine (CST) comes from the paper kraft pulp process where volatile materials are removed by applying heat and pressure. This source represents roughly 60% of available turpentine5 The third method relies on harvesting pine stumps left in the ground from the paper mills and can produce wood turpentine (WT) in limited quantities.
The composition of the pine tree exudates varies depending on the tree species and growth region. On average, exudates contain about 40% gum turpentine and 60% gum rosin. Being a labor intensive activity, tree tapping has been challenged by increasing labor costs. In addition, over the past few years, there has been a decrease in the demand for gum rosin (used as resins for adhesives, tires, etc.) as changes in market demand have pushed users towards hydrocarbon derived resins. Taken together, these changes are shifting industry attention to crude sulfate turpentine.
North America and Europe are the leading crude sulfate turpentine producing regions of the world. They are representing 59% and 33% of the softwood kraft production, respectively. For every 1,000 kg of paper produced from soft wood pine trees, roughly five kg of crude sulfate turpentine is obtained6 In addition to its use for production of aroma molecules, CST also forms a raw material to produce additives, adhesives, rubber and personal/home products. While the paper industry is commonly criticized for deforestation, it plants more trees than harvested in the United States every year7,8 In fact, more trees now grow in these areas than in the 1970s. Most paper mills in the United States ensure they are sourcing wood from farms that use sustainable forest management practice9 Forest certification programs, such as the Forest Stewardship Council (FSC), Sustainable Forestry Initiative (SFI), American Tree Farm System (ATFS) and Program for the Endorsement of Forest Certification (PEFC) ensure harvested areas can regenerate and continue to produce in the long term. In the United States, over 80% of trees harvested grow on private lands. The income landowners generate from softwood trees grown on their land encourages them to maintain and sustainably manage the resource. Sweden and Finland, major paper producers in Europe, also follow strict laws and high standards for forest management. They require that harvested forests can regenerate at a rate of two to three new plants for each harvested tree10 Proper forest management produces paper as one of the few truly sustainable, naturally derived products.
Initially, turpentine served as a solvent and disinfectant. Eventually, it was upcycled to produce aroma molecules. Today, it is gaining renewed attention as an alternative to some petrol fragrance ingredients. While some pine oils can be produced directly from turpentine, most turpentine derivatives require fractionation, purification and/or derivatization (F-1). For α-pinene and β-pinene isomers, the major fractions of turpentine, the exact amounts depend on both the tree species and growth habitats. For instance, in the United States, most of the crude sulfate turpentine contains a range of 60% to 70% α-pinene and 20% to 25% β-pinene, while in Northern Europe, it contains a range of 35% to 64% a-pinene and 1% to 22% β-pinene11,12
Kindly read the full charts on www.perfumerflavorist.com
α-Pinene and β-pinene also represent the most versatile fractions of turpentine. Some of the most known and used aroma molecules are or can be produced from those isomers. Using the Symrise process as an example, linalool and its derivatives, linalyl acetate and tetrahydrolinalool, are produced by a highly selective hydrogenation of α-pinene in the presence of a catalyst which gives cis-pinane. cis-Pinane then oxidizes to hydroperoxide. The latter is reduced to cis-2 pinenol, which then goes through pyrolysis to obtain linalool that is further processed into different products13,14 Today, most of the linalool and derivatives used in the market come from petrol, in contrast, Symrise makes it from α-pinene.
The isomerization of linalool results in nerol and geraniol, providing access to the entire group of its derivatives, citronellol, citronellal, geranyl acetate and tetrahydrogeraniol. Geraniol and its derivatives can also come from pinene or from petrol. Today, only around half of the geraniol and derivatives available in the market come from turpentine.
The pyrolysis of cis-pinane to dihydromyrcene, followed by a hydration step, results in dihydromyrcenol. It forms one of the most used raw materials in fragrances due to its characteristic citrus notes, cyclodumol acetate and tetrahydro-myrcenol. Different from linalool and geraniol, dihydromyrcenol and its derivatives can only be obtained from turpentine.
The pyrolysis of β-pinene creates myrcene, which forms the basis for geraniol and nerol, Dimethyl Myrcetone (Symrise), Iso E Super (IFF) and Menthol (Takasago).
What is described in this article is a fraction of the fragrance materials that are currently derived from turpentine. The versatile α-pinene and β-pinene, and smaller fractions such as methyl chavicol, provide ample access to numerous aroma molecules via environmentally sound procedures. In addition, to the current options, there are also future possibilities. New market landscapes and increased environmental awareness have placed turpentine at the forefront as an environmentally friendly alternative to petrol products while providing ample renewable options to the perfumer’s palette.
Kindly read the full references on www.perfumerflavorist.com