Industry News, Adhesives & Sealants & Tackifiers
Acrylic Adhesives: Leader Among Waterborne PSAs
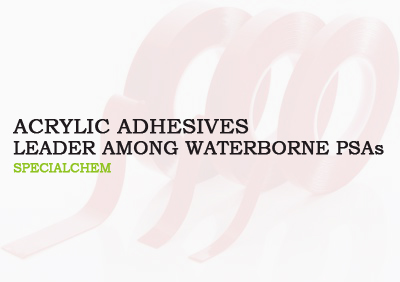
Industry News, Adhesives & Sealants & Tackifiers
Link: Acrylic Adhesives: Leader Among Waterborne PSAs | SpecialChem
By: Edward Petrie
Acrylic adhesives are noted for their versatility and scope. Acrylic adhesives are available as polymeric solvent solutions, waterborne emulsions, or as monomer mixtures, which may be cured by ultraviolet light, heat or chemical catalysts. The adhesives either cure in the bondline (thermosetting acrylic, cyanoacrylate, or anaerobic acrylic monomers) or from high molecular weight polymers that are formed outside the bondline.
Although acrylic polymers are used in laminating adhesives and construction sealants, the most common acrylic adhesive types used today are those that are available as water emulsions, and the most common application is in pressure sensitive adhesives (PSAs). They are thermoplastic systems that can be crosslinked depending on the requirements of the application. These waterborne PSAs will be the primary focus of this article.
Structural thermosetting acrylic adhesives have also been developed. Although these are outside of the scope of the present article, they have been well-defined and characterized in a recent SpecialChem article.1
Figure 1: Selection Tree for Thermoplastic Acrylic Adhesives ©Specialchem
By selection of the monomer and polymerization conditions, a great many acrylic base polymers are available to the adhesive and sealant formulator. Acrylic adhesives are generally prepared from copolymers or tripolymers. By changing the polymer structure in this way, the polymer properties can be engineered for a particular application. Homopolymers are not often used because they cannot provide the proper balance of tack, cohesive strength, and resistance to creep or flow that is required for most commercial applications.
Acrylic PSAs are produced mainly from soft monomers that have a low glass transition temperature (Tg) and a high level of molecular entanglement. These monomers are then copolymerized with other monomers to provide the necessary balance of properties. Some of the various monomers that are used in synthesizing the base polymers are characterized in Table 1. Some non-acrylic monomers, such as vinyl ethers and vinyl acetate, are also used in developing copolymers for acrylic adhesives.
Type | Characteristics | Monomer | Tg,°C |
Soft |
|
2-Ethyl hexyl acrylate | -65 |
n-Butyl acrylate | -50 | ||
Iso-octyl acrylate | -70 | ||
Hard |
|
Methyl methacrylate | 105 |
Methyl acrylate | 9 | ||
Vinyl acetate | 32 | ||
Styrene | 100 | ||
Polar |
|
Acrylic acid | 106 |
2-hydroxyl ethyl acrylate | -15 | ||
N-Vinyl pyrolidone | 180 |
There are a large number of acrylic base polymers available as different monomers and copolymers, which give differences in modulus, peel strength, and environmental properties. At room temperatures, these monomers are generally clear and colorless. In order to provide storage stability, stabilizers such as hydroquinone are added by the manufacturer.
Soft monomers will form PSAs with some degree of cohesive strength, but polar monomers are often added in order to provide a copolymer that can form hydrogen bonds and provide a higher degree of cohesion. The polar monomers also increase wetting and improve adhesion to low surface energy substrates. For higher peel strength, harder monomers with higher Tg are incorporated into a copolymer. Crosslinkable monomers may be included to make the formulated adhesive curable by catalyst, heat, or other energy source. Crosslinked adhesive films have improved shear strength and performance especially at higher temperatures; however, peel strength and tack are usually reduced.
A wide variety of monomer blends are employed to meet the requirements of various applications. Most PSAs have a soft monomer content of 70-90%, a hard monomer content of 0-30%, and a polar monomer content of 3-10%. However, a simple general purpose PSA can easily be produced from a blend of 95% soft monomer and 5% of a hard, polar monomer such as acrylic acid.
Waterborne acrylic PSAs are prepared by emulsion polymerization of acrylate monomers in water using emulsifiers and water soluble polymerization initiators. The resulting polymer emulsion (50-60% solids) is generally stabilized with a surfactant. Particle size of the acrylic polymer in emulsion is on the order of 0.1–.4 microns, viscosity is 100-500 cps, and Tg is approximately -50°C to +20°C.
A typical acrylic polymer for PSA applications is composed of the following elements:
Peel adhesion can be correlated somewhat with glass transition temperature. A polymer that is too soft and fails cohesively when peeled can be improved by copolymerization with a monomer that raises its Tg. Conversely a polymer that is too hard and fails in peel can be improved by copolymerization with a monomer that will lower the Tg.
In order to possess sufficient tack required for a pressure sensitive adhesive, the polymer must have a fairly low Tg. This is why both 2-ethylhexyl acrylate and butyl acrylate have excellent pressure sensitive characteristics without additives. Generally homopolymers with high Tg are not tacky enough and require copolymerization with other monomers of lower Tg.
The properties of a pressure sensitive adhesive as a function of molecular weight are illustrated in Figure 1. Both tack and resistance to peel increase with increasing molecular weight until a maximum is reached. The maximum is at a fairly low molecular weight, and the transition of the mode of failure from cohesion to adhesion takes place in this region. A further increase in molecular weight causes a decrease and leveling of these properties. Commercial adhesives are generally offered in this range of molecular weight.
Figure 2: PSA properties as a function of molecular weight (SpecialChem Fig. Ref.: PSA properties vs. mw) ©Specialchem
In some applications, acrylic adhesives do not require the addition of a tackifier to provide pressure sensitive characteristics. However, in most pressure sensitive applications, tackifiers are required to increase tack and peel strength and to improve adhesion to low surface energy substrates. Tackifiers are often used in acrylic emulsion formulations for paper labels, packaging tapes. Here a high degree of adhesion is necessary for difficult to bond substrates such as plastic film, bi-oriented polypropylene (packaging) tape, and the like.
Table 2 shows some typical properties for an acrylic PSA tackified with 40 phr of rosin ester. Notice that the tack and peel strength is increased significantly due to the addition of the tackifier while the shear strength is reduced. This is due to the lower modulus and softening effect of the tackifier. Tackifiers are sometimes also used to lower the cost of the final adhesive and are typically used at concentrations of less than 30-40 percent by weight.
Property | No Tackifier | Tackified |
Creep: shear hold (hrs), 1kg, 1″ x 1″ | <200 | 19 |
Creep: shear hold (hrs), 1kg, 0.5″ x 1″ | 50 | 4 |
Shear Adhesion Failure Temperature (SAFT), °C | 137 | 65 |
Probe tack (g), initial | 123 | 206 |
Probe tack (g), 72 hrs UV exposure | 117 | 159 |
Peel Strength (N/25mm) after 7 days of wet-out time:
|
15 7 |
40 20 |
Tackifiers with melt points substantially above the Tg value of the polymer can be expected to improve the strength of the adhesive at elevated temperatures but reduce the tack. Lower melting resins will impart greater tack and low temperature flexibility at the expense of creep and shear strength. Thus, the tackifier is responsible for the balance of tack, peel, and shear properties of the final adhesive, and very often tradeoffs in properties must be made.
Although tackifiers lower the modulus and provide a more flexible resin, they can often increase the Tg by reducing the rubber plateau. Since tack is measured as the force or energy to break, adhesives should have a high modulus at the strain rates and magnitudes imposed on them during rupturing of the bond. Tackifiers raise the glass transition temperature of elastomers so that the adhesive mixture has a high modulus at high strain rates and normal ambient temperatures. Thus, a tackifier increases the modulus at low temperature, short time, and high frequencies, but decreases modulus at high temperature, long times, and low frequencies.
Tackifiers used for acrylic emulsions need to be compatible with the base polymer and the surfactant package that is used. Pre-emulsified tackifying resins are available for waterborne systems. Rosin ester derivatives and some modified C5 /C9 hydrocarbons are often employed.
A plasticizer decreases both the Tg and the modulus of the adhesive. Esters, such as phthalates and adipates, are commonly used at concentrations of typically 2-5 percent. Because the adhesive is softened, tack is generally improved. However, plasticizers sometimes reduce peel strength, and this may be desirable to give a smooth release from a liner. Table 3 shows the results of adding a phosphate plasticizer to an acrylic PSA.
Amount of Plasticizer, phr | Peel Adhesion, g/cm width | Rolling Ball Tack, cm |
0 | 429 | 3.0 |
4 | 407 | 3.6 |
10 | 363 | 2.8 |
The primary difficulties with plasticizer are that they lower the Tg so that creep may be a concern, and they tend to migrate out of the bulk adhesive with time. Nonmigrating plasticizers are commercially available. Esters, such as phthalates and adipates, are commonly used at concentrations of typically 2-5 percent.
The main purpose of crosslinking is to improve the shear and creep resistance properties of a PSA. Noticeable improvements can be achieved even at relatively low crosslink density. However, crosslinking also decreases the elasticity of the polymer film with a resulting decrease in peel strength. Tack is usually also decreased.
In the polymerization of acrylates, multifunctional monomers or reactive groups carrying monomers can be introduced into the polymer chain for crosslinking. Divinyl benzene, ethylene glycol dimethacrylate, and similar monomers are used for this purpose. However, there are many different types of crosslinking reactions that can take place. Di- or multi-variant metal ions will react with COOH to form crosslinks. Polyfunctional aziridines will crosslink via the carboxyl group at room temperature.
Fillers can be used to extend the adhesive (i.e., to lower cost) or to change its properties. Clay, calcium carbonate and zinc oxide provide a moderate improvement in peel strength when added in concentrations of less than 100 phr of the base polymer. Zinc oxide, certain colloidal silicas, and other reactive pigments will significantly reduce peel strength when added at much smaller amounts.
Thanks to their broad formulation versatility, adhesives based on acrylic emulsion technology are suitable for high performance packaging, construction, medical, and many other applications. Permanent acrylic adhesive may require temperature, UV, and moisture resistance. However, adhesive properties can also be adjusted to allow for early removal or for repositioning.
Acrylic adhesives have excellent outdoor weathering and aging characteristics. One of their main applications is for outdoor graphics. Although they have lower adhesion than rubber based PSAs, acrylics have higher temperature stability and excellent UV resistance.
Acrylic adhesives tend to stick well to substrates such as metals, glass, and high-energy polymeric surfaces. Thus, they can be used for holding a wide variety of substrates including automobile identification tags, mounting tape, protective moldings, etc.
Many pressure sensitive acrylic resins provide excellent packaging and label adhesives at temperatures as low as –50°C. These are commonly used in the food processing industry. Depending on the properties of the base polymer and additive resins, these adhesive systems may be applicable to freezer conditions.
Acrylic tapes and label adhesives have medium water resistance, good resistance to oil and thermal shock, and poor resistance to organic solvents. Temperature resistance varies with the nature of the base polymer. They are especially well suited for outdoor applications (e.g., auto “bumper stickers”, identification tags, barcodes, signs, etc.). Acrylic tapes are used in high performance applications such as mounting tape.
As shown in Table 4, acrylic PSAs have a wider range of delivery options than other types of PSAs. Waterborne acrylic PSAs generally do not have the degree of moisture resistance as those acrylic adhesives that are available via solvent solution or UV polymerization. This is more related to the additives resulting from the emulsion polymerization process than to the base polymer itself.
PSA | Solvent Borne | Waterborne | Hot Melt | UV Polymerization |
Rubber (Styrene Butadiene Copolymer) | Good performance, high solids content | Not typical for styrene butadiene copolymers | Most common due to lower VOCs, equivalent in performance to solvent borne | Possible for crosslinking |
Acrylic | High performance | Most common, but poor moisture resistance | Developmental | Growing in popularity due to lower VOCs |
Silicone | High performance | Not available | Generally, not available | No (but crosslinking is possible via chemical means) |
UV curable acrylic PSA is gaining acceptance in the industry. Acrylic hot melt pressure sensitive adhesives (HMPSA) are also relatively new to the industry. Acrylic HMPSAs provide better oxidative resistance and UV stability than other hot melt or pressure sensitive adhesives. These adhesives can be applied as a hot melt, but once on the substrate they act as a pressure sensitive adhesive. In this method of application the use of solvent simply as a carrier to apply pressure sensitive resin to the substrate is eliminated.
Copyright of this article by Specialchem. We are sharing and promoting the market innovation.
If you like this article, kindly to visit adhesives.specialchem.com